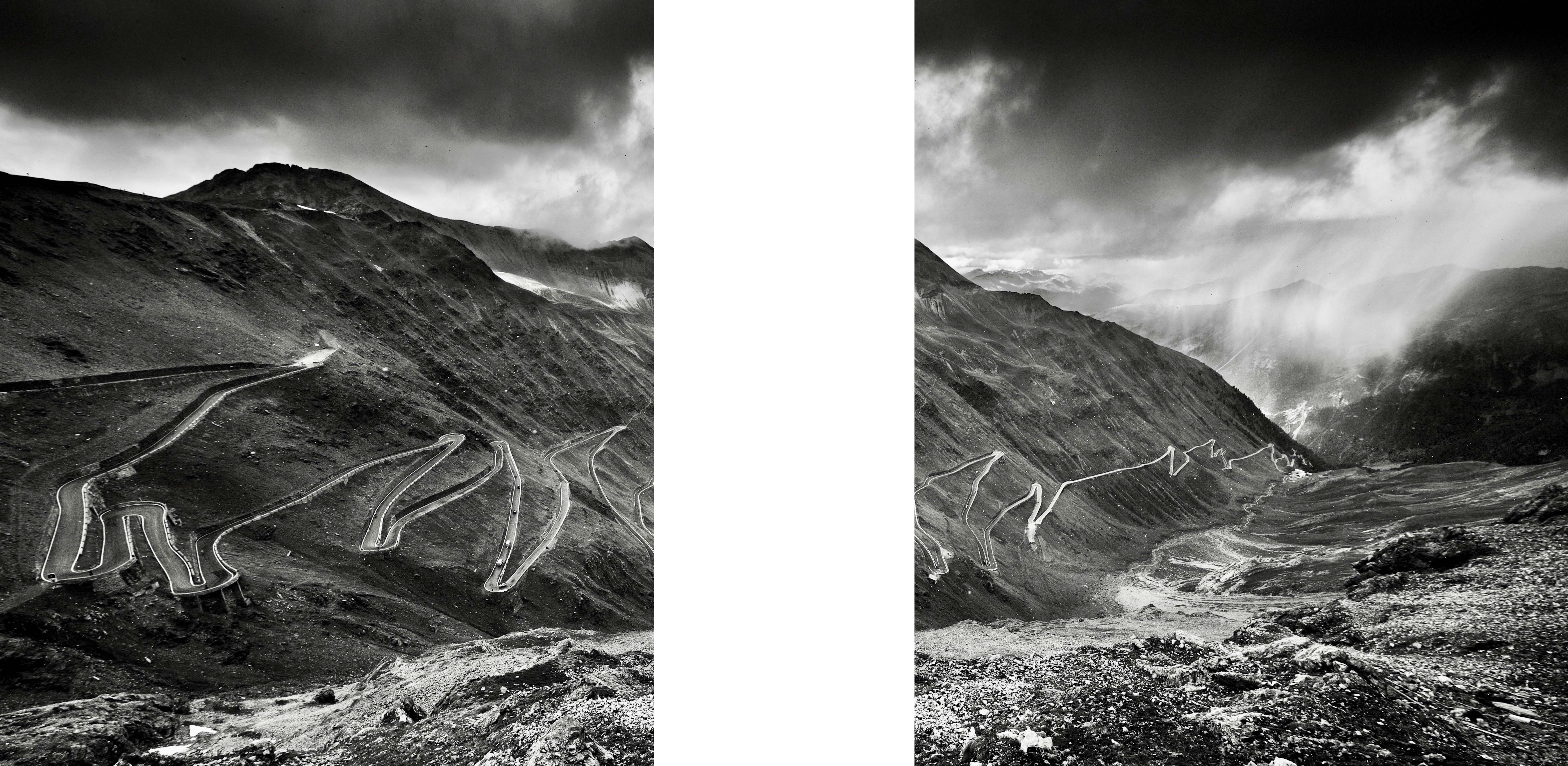
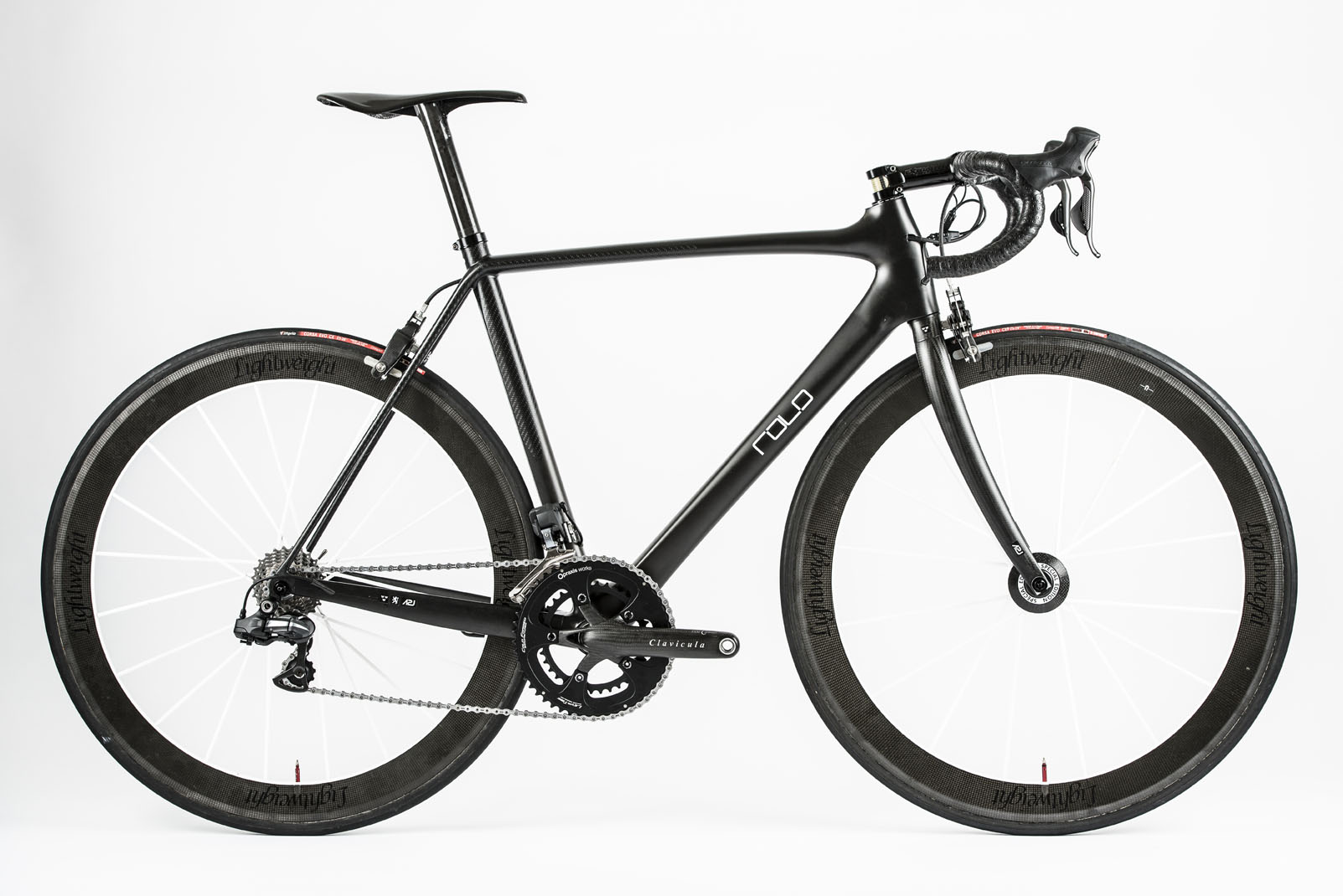
Super exclusive, super expensive and super spectacular are just three superlatives that come to mind when ogling ROLO’s custom carbon road bike, as seen at this week’s Cycle Show in Birmingham, UK.
Adorn with all kinds of goodies from the likes of Tune and some unknown brand of “unobtanium” carbon wheels, the bike dazzled onlookers as it stood poised on display at Fabric’s booth.
For those unfamiliar with the brand, ROLO is a Swedish based company that turns out very limited numbers of bespoke carbon framesets, which are handmade in Würzburg, Germany. And, as one might expect they come at a premium price.
Overview
Rolo is proud to announce our latest generation bicycle frame. As with the original, limited edition frame, our overarching focus remains on fit and handling. We have focused a great deal of attention on the front geometry for the bicycles and are the only carbon bicycle frame manufacturer to offer correct handling. Our bicycles exhibit quick and snappy handling at low speeds but become increasingly stable as speed increases. The result is that they require no course corrections through turns, and hairpins in particular, meaning that the rider can take a wider radius through the turn with complete confidence. The wider radius allows for higher speed at entry, through the turn and importantly at the exit.
We continue to be the only bicycle manufacturer to offer Ridertuned™ bespoke carbon lay-up and tailor the frame’s performance to the rider’s specification, with world leading weight and stiffness performance. Our frames weigh from under 620g in the lightest lay-up in the smallest size to just over 760g in the stiffest version in the largest size.
We remain the only manufacturer to offer completely consistent stack to reach ratio geometry frames across sizes. Our second generation frame also incorporates a number of upgrades and special features, such as a tapered head tube, our own proprietary bottom bracket assembly which allows riders to use any 24mm or 30mm axle crank without adapters, special very long life SKF bearings, and a 27.2mm seat post which is more comfortable and lighter. We have placed specific emphasis on everyday usability, durability and reliability.
The frames are manufactured by hand in Würzburg Germany. We source some of the highest specification carbon fiber prepregs available, including M55J, with a bespoke resin system. Once the carbon has been cut, each frame requires approximately sixteen hours of work to lay-up in the mold.
As another industry first, we can now offer the ultimate in custom manufacturing for the most discerning rider: a custom geometry homogeneous structure monocoque and custom lay-up frame. Never before has any manufacturer offered a custom geometry, true monocoque frame or even a custom lay-up. Based on a careful study of the customer’s size and fit characteristics, we offer a custom design and engineering process culminating in the production of a set of molds specific for the customer. While the cost of the first frame a customer orders will be more than one of our stock geometry frames, the subsequent frames, regardless of lay-up and performance level, will be substantially less.
The reason we chose to design and manufacture our own bottom bracket is that the bottom bracket is the true heart of the bicycle. We wanted to have a system that would accommodate a broad range of cranksets, that would be easy to change, that would not require adapters and for which we could source the best bearings available. We also make a pf30 compatible bb so a rider can switch the bb system without needing to use adapters on the frame.
The bearings we use are SKF Explorer series. In the 30mm axle series, which are 7mm wide, they have an effective life of 30,300 hours with a 500N load at 90rpm in 30C temperature. For a rider who rides 5 hours per day, 365 days per year, it will take over 16 years before the bearings fail. For the 25mm axle variant, where the bearings are 9mm wide, the useful life increases to 109,300 hours.