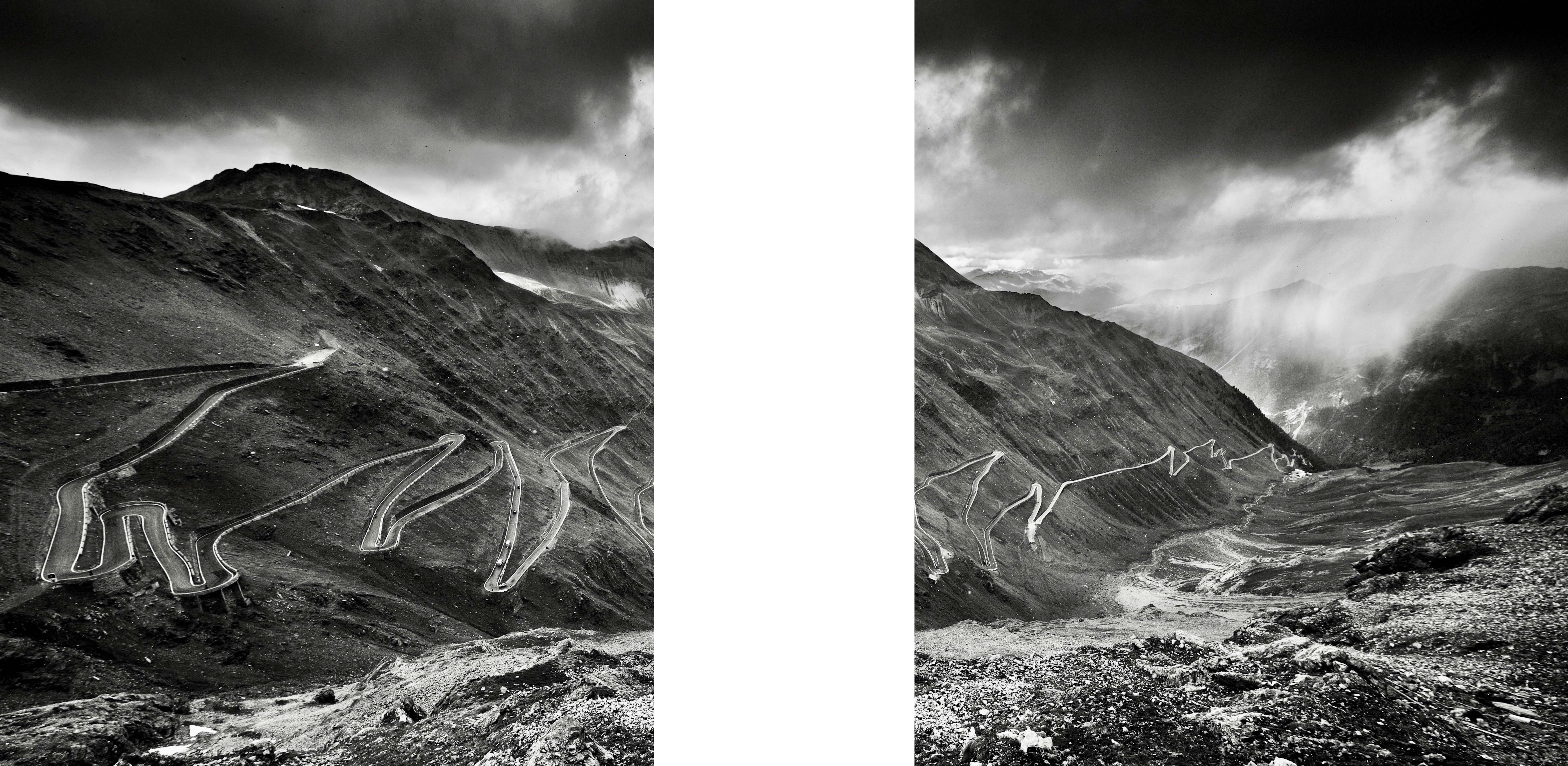
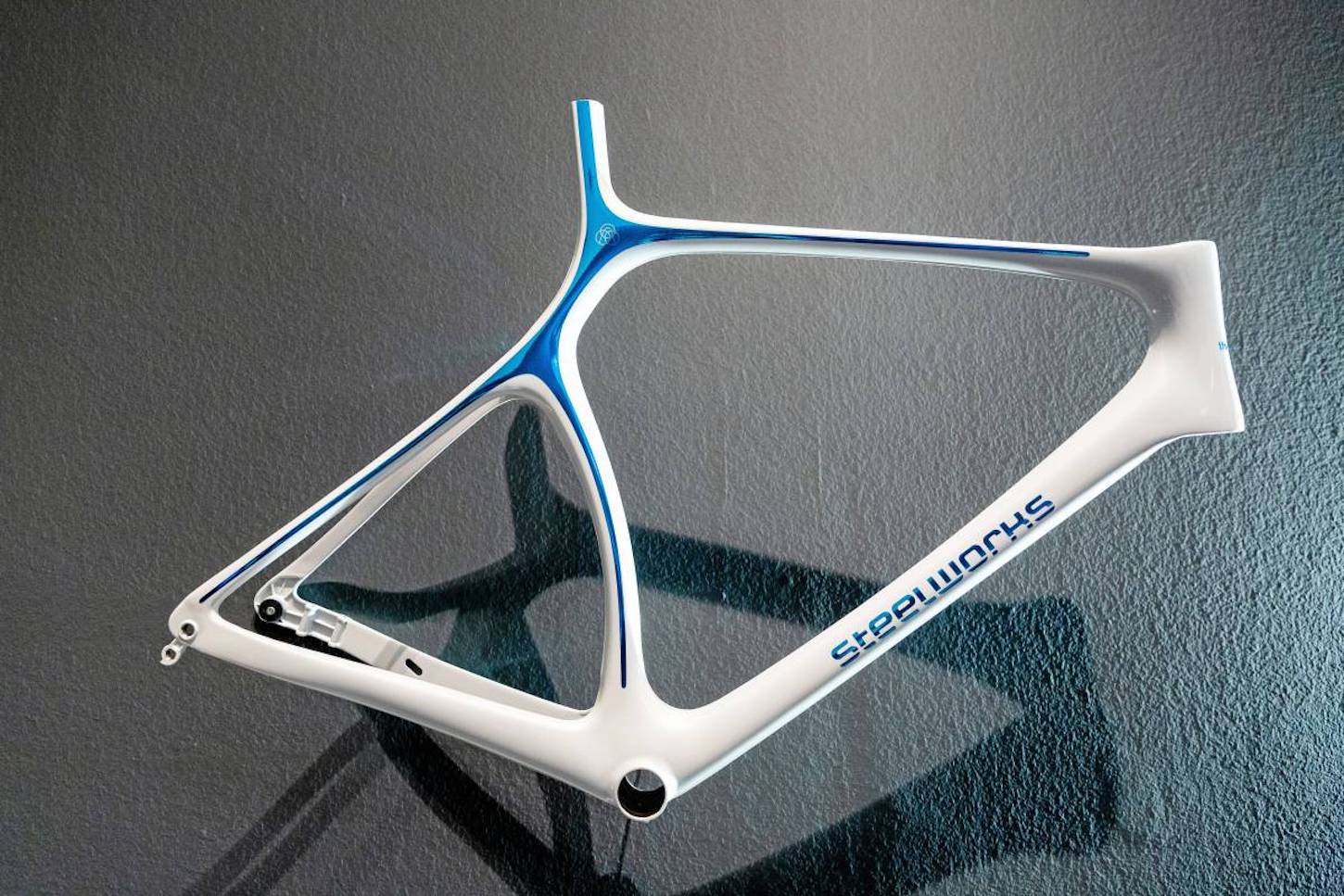
Rocketing eBike sales in Europe have caused a scarcity of available materials in the bicycle industry, particularly aluminum, forcing some companies to look into alternative sources of “metals’.
Since the production of aluminum frames can be complicated, many brands have turned to steel as a potentially viable alternative. However, there’s no going back to chromoly tubing. But, rather the quest for a new highly durable grade of steel with higher strength and stiffness than aluminum with the forming capabilities of carbon fiber.
Steel instead of aluminum is the solution for quickly increasing production in Europe, points out production expert Luigi Seghezzi, forecasting that within the next 3 years some 3 million eBikes frames will be made in Europe. He expects that the biggest part of the 3 million frames will be made with what he referred to as ‘light metal’. Asked whether this means the return to ‘old school’ Reynolds double or triple butted tubing, his answer was no. It will be a very new type of light metal which will be matching the lightweight characteristics of aluminum frames.
In response to the growing need of a new material, the world’s leading steel supplier, Thyssenkrupp Steel, has revealed a new steel that’s already getting a lot of attention as evidenced by the company’s recent Red Dot Design Award.
“Dual-phase steel, an advanced, highly durable steel that has a higher strength and stiffness than aluminum and the forming capabilities of carbon materials. The galvanized steel sheet is initially formed into two half tubes which are then welded together in an automated, high-precision 3D laser welding process. This technology, otherwise used only in the high-tech industry, produces virtually invisible welds of consistent high-end quality for bicycle frames and demonstrates the completely new design possibilities offered by steel. The extremely high stiffness of the steel frame in the area of the pedal bearings ensures optimum power transmission and assists propulsion. At the same time the high flexibility of the saddle tube and the intrinsic damping properties of the material make for a fatigue-free, comfortable ride,” says Thyssennkrupp Steel.
Thyssenkrupp Steel, which employs about 27,000 employees and has a yearly turnover of 9 billion euros in sales also points out, “modern bicycle frames are generally made from aluminum tubes or carbon fiber laminates to achieve high stiffness, though this inevitably comes at the cost of comfort. This was the starting point for steelworks. We took inspiration from the diverse properties of steel. Without the high strength of steel, the bionic design of the saddle tube would not have been possible,” says Jia-Uei Chan, leader of the steelworks project. Using thin steel sheet and state-of-the-art production processes, steelworks breaks with the conventions of customary frame manufacture to combine the otherwise conflicting design demands of stiffness and comfort.”
It will be interesting to see if Thyssennkrupp Steel’s new Steel Works division can put its stamp on the phrase “steel is real” with a modern-day version of the material that can reestablish homogeneity to Europe’s once thriving frame industry.