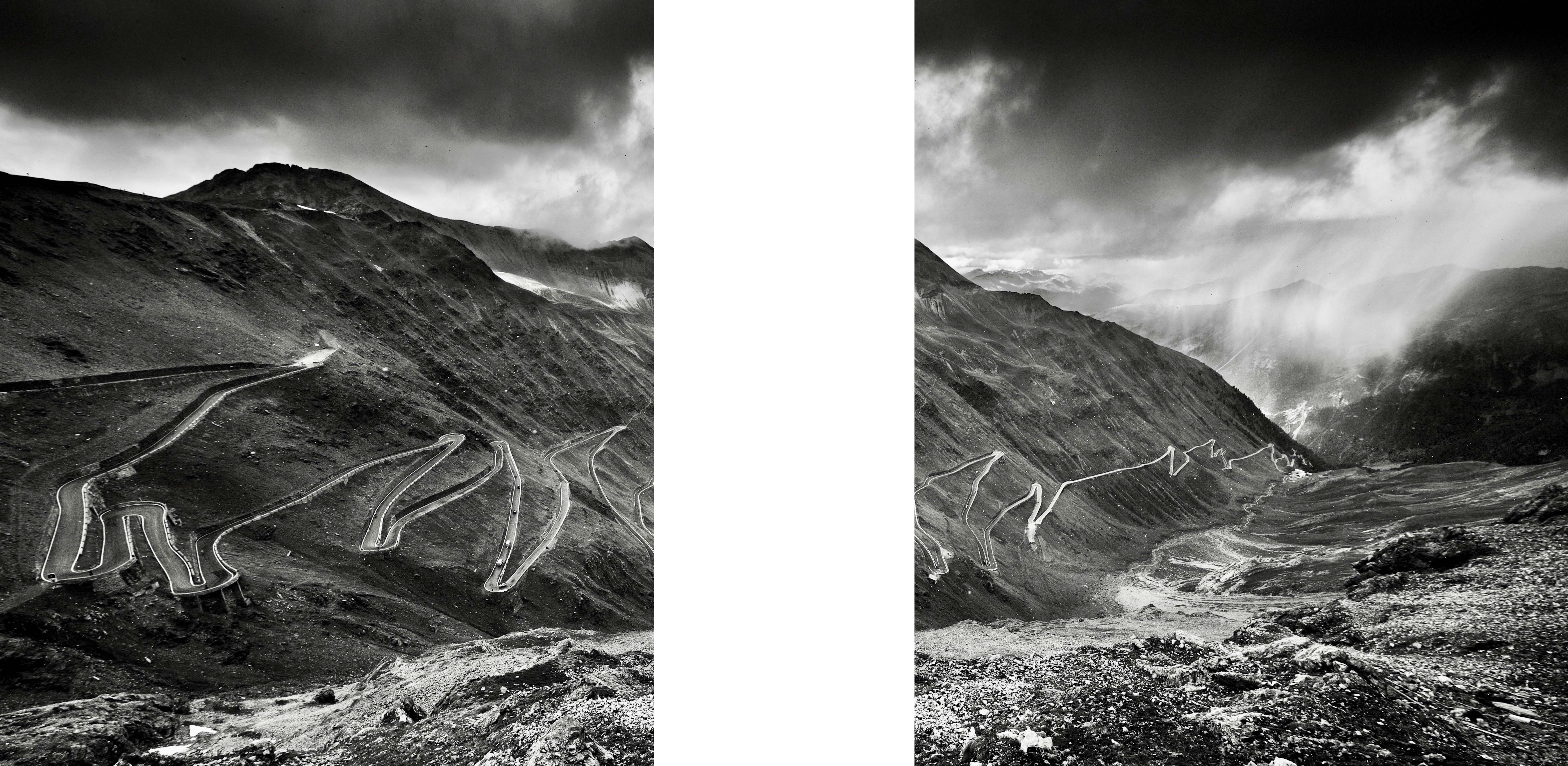
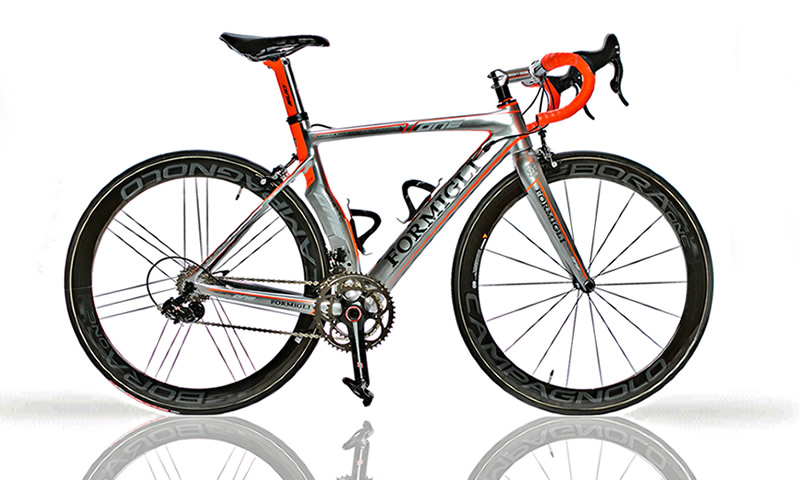
Is it a road bike ? An "aero" bike ? Or, a Gran Fondo bike ? According to the Italian brand, Formigli, it’s all of those bikes in one.
Indeed, after two years in the making, Renzo Formigli is calling his new road bike the "One".
Here’s why:
Do you feel buried in choices among carbon road bikes? Formigli has made it easy for you. This is The ONE. The only road bike you need.
Renzo Formigli calls this new bike, two years in the making, The ONE. There is no other bike like it. It’s not just the highest performing racing bike Renzo has ever made, magically it is also his most comfortable for gran fondos and club rides.
Those two qualities were thought to be mutually exclusive in one frame: rigidity, thus responsiveness, and comfort.
How did he do that?
First, the T 800 carbon Renzo chose for THE ONE allows him to build-in flexibility at specific points on the frame. Previous carbons denied him that control. Thanks to the new carbon, Renzo found he was able to use new tube shapes, diameters, and angles throughout the frame as never before.
Compared to previous Formigli frames, the upper tubes (the top tube and seat stays) are smaller. The lower tubes (the downtube and chainstays) are larger in diameter. Renzo changed the steerer tube (at the top of the fork) to 1 ¼” from the 1 ⅛” steerers on our other frames. The new steerer not only provides increased stability downhill at speed, the difference is dramatic when you’re all-out in a sprint or hammering on a climb.
Note The ONE’s seat tube. It’s arc shape creates a half-fairing; it helps to decrease the airflow disturbance caused by the rotation of the rear wheel. And the increased size of the seat tube leads to a significant reduction of the twisting forces exerted on the frame as you hammer the pedals. To achieve just the right amount of flex in the rear, for comfort and rough-road traction, he fattened the chain stays and slimmed the seat stays, lowering the seat stays’ placement on the seat tube to decrease the angle of the rear triangle.
The new carbon, the new tube sizes and the revised frame angles work in concert to combine rigidity and comfort.
Specifications
- Frame Material High modulus carbon Carbon fabric constitutionT 800 high modulus multi layered, uni and bi directional carbon
- Head Tube Integrated conical base bottom 1/2 top 1/4 Headset Integrated headset 1" 1/8 top – 1"1/2 bottom 45°. Included with purchase of frame set.
- Fork High Modulus 1/2- 1/8 Seat post Non integrated. Included with purchase. Painted to match frame, no additional charge.
- Seat post diameter Frame compatible with seat post diameter 31.6 tapered seat tube
- Front Derailleur Braze on Dropouts material
- Carbon Drops Raw weight of frame 1240-1320 g
- Bottom bracket Press Fit 86.5 x 41
- Optional Electronic shifting Di2 or EPS ready. Prepared for both electronic and mechanical.
- Electronic: battery optional inside seat post. Cables Internally or externally routed
- Top tube Sloping Size Made to order see geometry chart
- Paint Standard color see color option chart Finish Matte or glossy Paint options Send Formigli a .jpg of desired color or choose a standard paint scheme color from above images.
- Custom paint scheme additional charge.
- Additional custom decal additional charge.
- Brakes Disc brake option available with modified fork
Geometry
Size CT CC TT TH SCO TL CL FC SAº
42 Custom Custom Custom Custom Custom Custom Custom Custom Custom
45 Custom Custom Custom Custom Custom Custom Custom Custom Custom
48 Custom Custom Custom Custom Custom Custom Custom Custom Custom
50 Custom Custom Custom Custom Custom Custom Custom Custom Custom
52 Custom Custom Custom Custom Custom Custom Custom Custom Custom
54 Custom Custom Custom Custom Custom Custom Custom Custom Custom
56 Custom Custom Custom Custom Custom Custom Custom Custom Custom
58 Custom Custom Custom Custom Custom Custom Custom Custom Custom
60 Custom Custom Custom Custom Custom Custom Custom Custom Custom
CT Seat tube length (centre to top)
SCO Seat cluster offset
CC Seat tube length (centre to centre)
CL Chainstay length
TT Top tube length
FC Front centre
TH Top tube length (horizontal)
TL Tube length
SAº Seat angle
CARBON FRAME CONSTRUCTION
To design a brand new frame design, Renzo starts by drawing the frame concept by hand, then, with the carbon engineer, he analyses each tube’s shape and its performance with engineer to decide each tube’s final design. Next, a shop in Florence produces the proprietary molds. Our carbon tubes are then produced using these molds by a specialist company in Florence that also makes carbon fibre parts for Ferrari and Ducati. Each Formigli model has its own tubes.
Next comes the process of building a custom frame for a customer. First we get to know the rider and his/her wishes. We take measurements. Then we do a computer generated design of the frame to be constructed. We mock up a graphic file if a custom paint scheme is requested. The tubes are made. The tubes are cut and put in a mask by Sergio, Renzo’s uncle, and bonded. The tubes are next sent to our carbon shop in Modena, where the lugs are wrapped in carbon, and then bonded together in a process called sottovuoto, forming a much stiffer frame than a monocoque.
Next, the tubes are filled with sand and placed in a plastic vacuum bag. A proprietary vacuum sealing technique is used for the curing process. The sand prevents deformation of the tubing during the heating process and the vacuum creates a space devoid of air.
After the frame is prepped, it is heated to precisely 248°F for an hour, then slowly returned to about 100°F over a period of ten hours. Once removed from the oven, the bag is inflated, the frame is removed and the sand is cleaned out.
Once the finished frame is cured it goes through a meticulous sanding process. The joints are then polished by hand – so time consuming that mass-produced frames are not made using a tube-to-tube process because it takes four times longer to make a Formigli frame than a monocoque.
The final stage is the application of a resin like substance that seals the porosity of the carbon and readies the frame for painting.
The frame is then sent to Antonio, our painter, in the countryside outside Florence. The frame is further sanded and prepared for the paint process. The paint process takes approximately 12 hours. Each frame is painted by Antonio, from start to finish for consistency.
We develop the graphics and colours with the client. . The painter uses a complex Aereographe process to achieve the client’s exact colour choice. Customers are not limited to just a few color options, instead Formigli can paint a frame any color variation desired.
Formigli builds every frame with a tube-to-tube construction process. Building tube-to-tube allows for the creation of a custom frame based on each individual’s specific body measurements. Tube-to-tube design also enables us to use superior carbon that varies in layers and composition.
In contrast, 98% of other road bikes are now made in Asia–using a monocoque mold process, which takes hours to produce and paint a frame versus Formigli’s process which takes 6-8 weeks.
http://www.formigliusa.com/cm/Bicycles/Carbon-Road/ONE.html#.Uoz9pxbZaRl