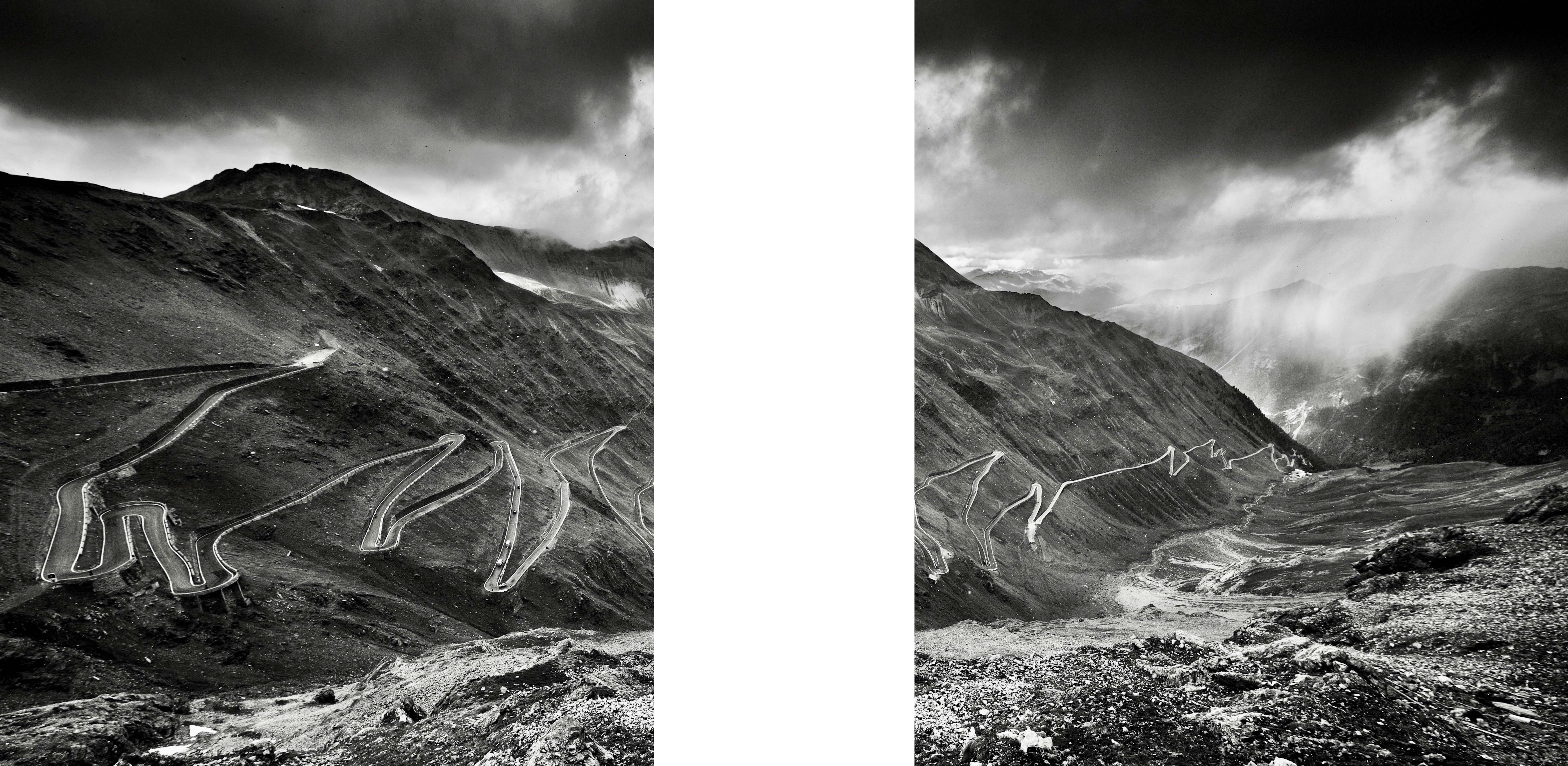
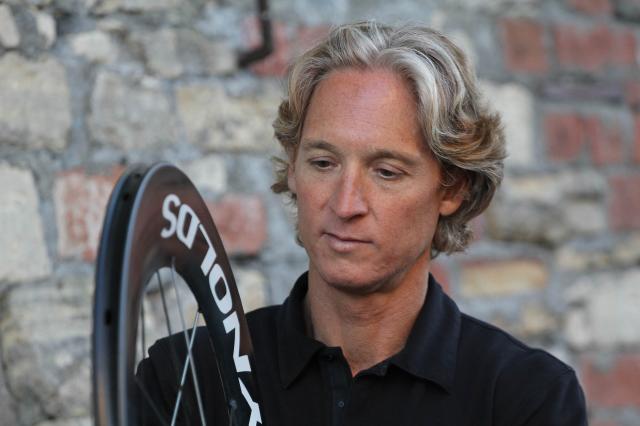
UNDERSTANDING WHEEL DYNAMICS: CARBON FIBER VARIABILITY
By Paul Lew, Director of Technology & Innovation
Reynolds Cycling, LLC
Welcome back to our series on wheel dynamics. This is my third article; the two previous have discussed spoke crossing and wheel stiffness. Here in part three, I’ll discuss the variability of carbon fiber as it pertains to bicycle wheel dynamics.
While the information here is specific to Reynolds’ bicycle wheels, the material specifications can serve as a reference for understanding the materials in most commercial carbon recreational components.
I’ll start by saying that it can be difficult to understand the material science of carbon fiber. Unlike metal that is produced as a standard alloy such as 6000 series or 7000 series, carbon fiber lacks a common standard. This presents challenges, but allows a tremendous amount of customization. Reynolds embraces the infinite combinations of carbon fiber lay-up and resin combinations, and assigns different formulas to each unique area of the rim – our MR5, CR6, and PR3 technologies.
Another complexity and another way in which metal and carbon fiber differ is that carbon fiber requires a “system” of both carbon and resin to bind it. Here’s more detail about the two elements:
- CARBON FIBER is known to design engineers as “reinforcement”. It is typically categorized according to stiffness, and measured in “modulus of elasticity” or MSI (referring to million pounds per square inch). “Modulus” is graded as follows:
o Low Modulus < 33 MSI
o Standard Modulus 33-34 MSI
o Intermediate Modulus 42-43 MSI
o High Modulus 55-70 MSI
o Ultra High Modulus 70+ MSI
As a general rule, as the modulus increases, the strength decreases and the fiber is more brittle. The grades of modulus that are associated with “best practices” for bicycle wheel production are ‘Standard’ and ‘Intermediate’.
- RESIN is the adhesive that bonds the carbon fibers together. There are many characteristics that design engineers examine to determine the suitable chemistry such as short-beam shear, and peel strength; however for rim brake design the Tg has become the overwhelming consideration in resin selection. Tg, or Glass-Transition Temperature, represents the point where the resin system begins to lose strength. Exceeding the Tg can result in rim warping.
While the two requisite components are carbon fiber, or “reinforcement”, and resin, there are several options for each that are used in the design process.
Let’s look at one of Reynolds’ carbon fiber and resin specifications and discuss further:
XYZ123-34-700-120G-R/C33%+/3%
Translation:
- XYZ = Manufacturer’s reference code
- 123 = Numeric code for the resin system. This code is cross-referenced to the resin properties
-
34 = Standard Modulus carbon fiber reinforcement
- 700 = Typical tensile strength (Ksi), in this case 700,000 pounds/ square inch
- 120G = 120 grams/ square meter is the weight of the material (120G is 0.0035 inches thick)
- R/C33% = Resin Content (this is the percent of resin vs. percent of reinforcement)
- +/-3% = Variability (tolerance) of the resin content. This means the true resin content for this specification can range from 30% – 36%
In addition to the modulus and strength of carbon fiber, the design engineer must determine the appropriate weight and thickness of each individual ply. This is determined based on aerial weight.
Aerial weight can range from 35 grams per square meter to 300 grams per square meter. Reynolds uses a range of aerial weights between 55 and 150 grams per square meter. These aerial weights range in thickness between 0.0015 inches and 0.0045 inches. Typical rim sidewalls range between 3 and 6 plys. A spoke face/ nipple bed ranges between 70 plys and 25 plys.
The resin used by Reynolds Cycling is a ‘hot melt’ system that is metered onto the unidirectional reinforcement. The sum of reinforcement and hot melt adhesive is known as pre-pregnated, or “pre-preg”. Pre-preg is the most accurate form of raw carbon and resin. Unlike “wet” resin (liquid resin brushed or rolled on to the dry carbon fiber), pre-preg is computer-metered to a precise specification and tolerance.
Reynolds specifies its pre-preg as a “net-resin” system. This means that the amount of resin in the pre-preg system has been metered accurately so that there is no extra resin left over after molding.
Creating the specification for net-resin molding is complicated, but determining the net-resin specification enhances productivity tremendously. Excessive resin generates high labor times for clean-up, while insufficient resin results in dry fiber (fiber that is not fully coated with resin, resulting in low strength).
From the material specification perspective, this summarizes the basics of carbon fiber design – but material specification is only one part of the equation. The other key component is the molding process, which is a labor of love requiring both artistic skill and a precise scientific understanding of pressure, time, and temperature.
We’ll explore the carbon fiber molding process in a future article.
http://www.reynoldscycling.com/reynolds/news/Understanding-Wheel-Dynamics:-Carbon-Fiber-Variability