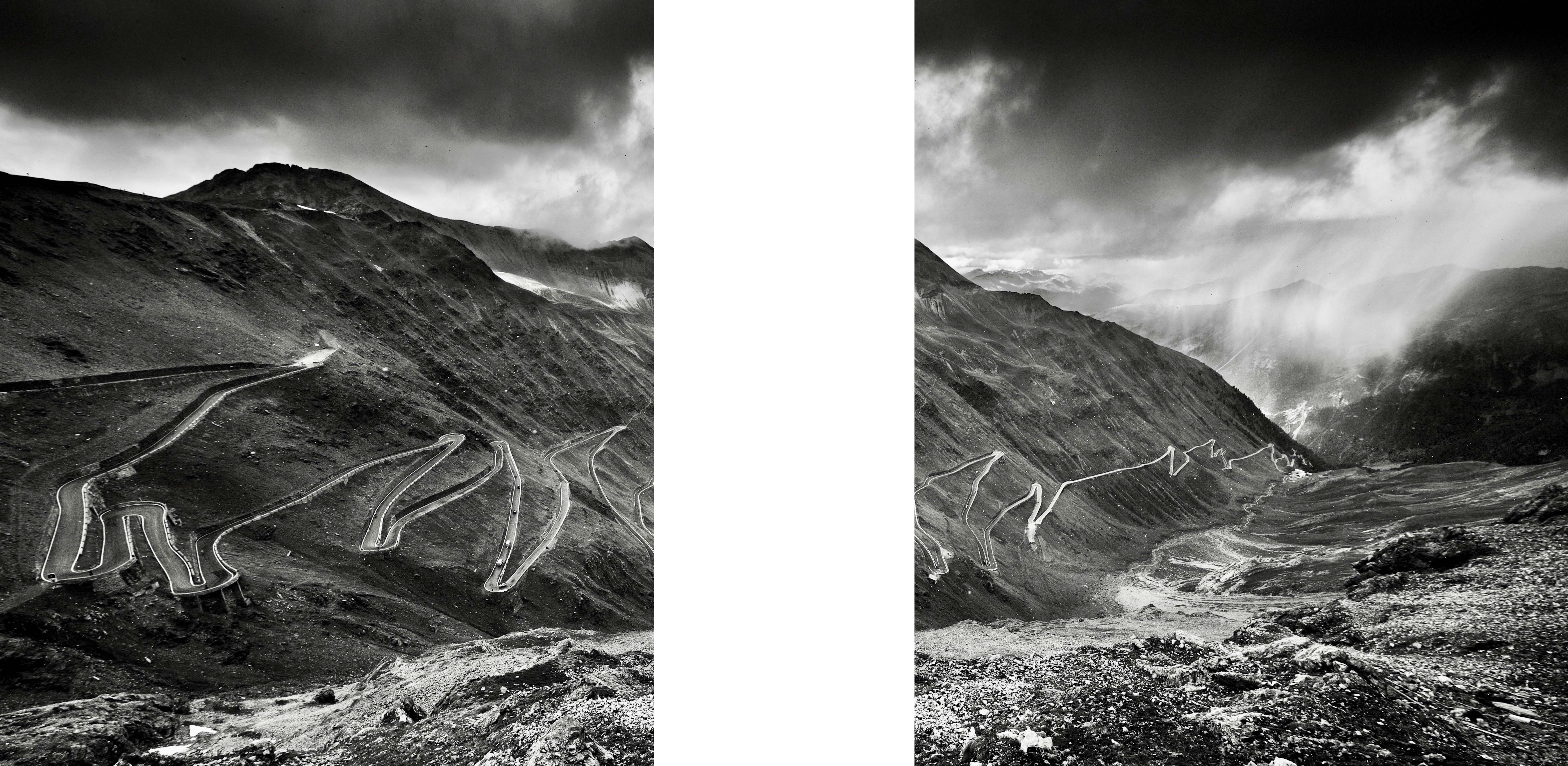
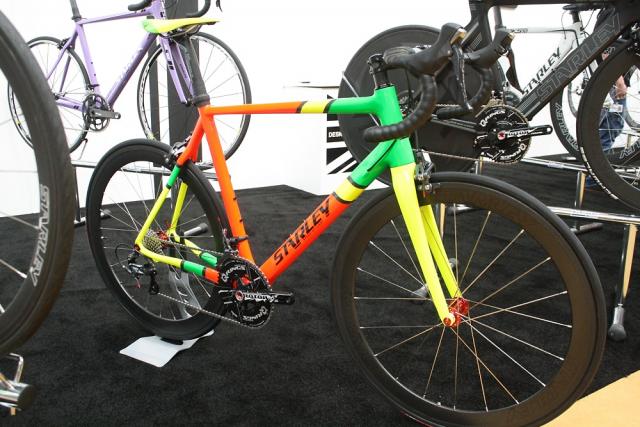
All Starley designs are based on carbon monocoque construction rather than carbon tubes and lugs as Starley believe it makes for a stronger and lighter build. Minimum frame size options are 3 no. on Mountain bikes and generally 5 no. on road and TT frames. Starley use carbon fibre because it is currently by far and away the best material to build high strength lightweight frames and components from.
However, the world of engineering materials never stands still and current developments being monitored are :-
Many structural components will soon feature automated laser manufacturing allowing engineers to explore completely new concepts with carbon fibres bound in thermoplastic polymer matrices, such as PEEK (Polyether ether Ketone), which melt at high temperature (around 400°c). Thermoplastics can also be recycled more effectively to reduce the environmental impact of manufacturing virgin composite materials.
F1 teams and aerospace companies are already testing parts that change shape in response to the loads places upon them (known as structural morphing). Viable profile components and frames that automatically adapt to aerodynamic conditions could be a direct offshoot of this cutting-edge technology.
Academic papers and patents promise composite materials that create strong optical, electrical, magnetic or thermal properties as well as high stiffness and strength values. Self-powering lights, energy regenerative braking or parts which monitor themselves for damage are being prototyped in other industries.
By including small ceramic fibres which extend and contract with applied voltage (called piezoelectric ceramics) at strategic points, researchers have cancelled out vibrations transmitted through a handlebar. A seat post is the logical next step.
Starley reduce weight wherever possible by considering every component in detail and through these marginal gains, Starley Bikes are noticeably lighter than its competitors at almost any price range but without compromise for safety. A JKS-R1 54cm bike for example with a 2012 Red build weighs 6.5kg excluding pedals but the frame, which weights 1.05kgs, is superbly rigid. The current
UCI race legal limit is 6.8kg which leaves plenty of scope to add a power meter and bike computer.
Wherever possible, Starley works with British and European partners including USE, Royce, Sapim, Fibrax and Fizik, but as the technical expertise of working in volume with carbon fibre in this industry is limited in the UK, we are obliged like virtually all other high end bike manufacturers to have the Starley auto-cad designs manufactured to detailed specifications abroad.
Starley work very closely with two composite specialist companies with the proven expertise of working to exacting standards with carbon fibre, one in mainland China, the other in Taiwan.
All Starley frames and components are rigorously lab tested in the UK to EN14781:2005 racing bicycles and EN14766:2005 mountain bicycles as appropriate. Starley products are fully road tested in the UK by team riders and their feedback taken into account by the product development team before any frames, wheels or components are available to purchase. EN14781 is the toughest standard for road bicycles, and comprises a total of four test clauses for bicycle frames: two impact tests and two fatigue tests involving 100,000 test cycles.
Whereas manufacturers commonly choose to perform each test clause on a different sample, we’ve elected to have an impact test performed following fatigue testing for each frame. We’ve also opted to test using a rigid dummy fork so all test forces are transferred to the frame, rather than being partially absorbed by a compliant actual fork. Samples are tested for durability, crash worthiness and stiffness before being test ridden for ride quality.
All Starley products are received into the UK in a raw carbon state. That way, all aspects of the carbon fibre frame and component build can be properly quality checked. Only following these checks including correct alignment, are they introduced into the UK production line.
The carbon fibre is then prepared by hand to receive an initial coat of primer. Once this has dried and the appropriate finished artwork produced by the Starley graphics department, then the paint and decals are applied by hand before receiving final coats of protective UV lacquer and a subsequent quality check.
All Starley bikes and components are then fully built up in the UK by Starley technicians and mechanics and quality checked prior to being available for sale. All in all each product goes through a five stage UK quality control program before departing for the customer. It is this level of quality control and confidence in the products which underpins the five year frame-set warranty and two year component warranty that comes with a Starley bike and the individual Starley components.
Carbon fibre composites currently offer the best weight, stiffness, durability and ease of use parameters out of all other materials available for bicycle component manufacture. Composite literally means of several materials – in our case carbon fibres and resin.
Carbon fibre layup and the quality of manufacture is extremely important in being able to control torsional load. Carbon fibre composites are a man made material that can be made to satisfy virtually any mechanical property without changing the overall structural shape of the part.
The main suppliers, representing 70% of the total market, of the type of carbon fibre used for the manufacture of bicycle parts are Toho Tenax, Torayca Industrial and Mitsubishi Rayon, all based in Japan. They are the main suppliers in what is called normal tow (under 12000 fibres) carbon fibre or commonly known as 1k, 3k, 12k weave and UD carbon fibre.
The sports sector represents only 20% of the total carbon fibre consumption, with bicycle parts manufacture therefore probably representing only 5% of the global consumption of carbon fibre. This means the carbon fibre materials and associated resins that the bike industry is using were originally developed for another sector such as aerospace.
Starley generally use Torayca T700s, T800H and T1000G.
The carbon fibre that is used comes in rolls of pre-impregnated fabric, or prepreg. Since carbon fibre composite is a composite material that combines carbon fibre and resin, prepreg means that the carbon fibre has already been saturated with resin. How much resin is present and what type it is depends on the grade and end use of the carbon fibre prepreg.
Bicycle components, specifically bike frames are made using various grades of carbon fibre characterised mainly by their tensile strength and tensile modulus. Tensile strength is the amount of force needed to cause the fibre to break, while the tensile modulus is a measure of the carbon fibre’s stiffness.
The cost of the materials generally go up with the increase in tensile strength or increase in tensile modulus. The tow (weave) also determines the cost of material with larger tow prepreg (e.g.. 12k) costing less due to the lower cost of manufacture.
Tensile strength and tensile modulus are almost inversely proportional, that is as the fibres become stronger in tension and resistant to breakage, they become less stiff. In bike frame manufacturing, this means that at present it is not possible to construct an exceptionally light frame (below approx. 850g) out of carbon fibre composite which is at the same time stiff and resistant to spontaneous cracking and damage in case of a fall. Starley frames use multiple layers of varying modulus carbon fibre in specific areas of each frame size in order to achieve the desired stiffness, weight and durability.
Carbon fibre prepreg cloths of varying modulus and tow are cut into smaller patches according to the layup chart which varies for each frame model and size. Starley layup is optimised to handle specific directional loads acting on the frame.
Laying down patches of carbon fibre prepreg in different orientations is important because carbon fibre always has maximum strength along the lengths of the fibres. This also helps illustrate why using uni-directional fibre instead of woven carbon fibre (e.g.. 1k, 3k, 12k) creates stronger frames. When using woven carbon fibre, at any one time half of the fibres are not oriented so that the force acts along their length. Of course, using multiple layers of woven carbon fibre in different orientations helps mitigate this and can be used to create a more forgiving frame ride.
The main use of woven carbon fibre in bicycle frames can often be solely for appearance. 1k, 3k, or now more rarely 12k carbon fibre can be specified on the surface of the frame. Starley use unidirectional carbon fibre and 3k woven carbon fibre when it has clear structural or mechanical benefits only.
Starley manufacturing techniques produce a highly compacted laminate that gets the most performance from high modulus carbon fibres through optimum placement without fibre damage or kinking.
The entire frame is laid up in a custom shaped mould. There are no tubes, just hollow carbon profiles that handle all the loads. Monocoque construction is Starley’s preferred method for working with man-made composite materials. Because carbon fibre can be laid up precisely as desired, any shape and performance parameter can be obtained through a combination of layup and shape of the mould. There are no practical construction factors that influence the final shape and performance, thus even the most carefully designed lugged or bonded tube frames are inferior in this regard.
There are several methods of making sure that the various layers are tightly packed together. This is generally accomplished by inserting air bladders into the laid up, raw frame and inflating them once the frame is placed in the mould, prior to baking. This is still how carbon monocoque frames are made. The disadvantage of the common air bladder method is that due to the relatively low pressure applied and complexities of the shapes being moulded, wrinkles and voids where air remains trapped between layers are relatively common. This makes the frame weaker.
Starley use special polymer bladders which are inflated to a higher pressure and use specific solid silicon forms in key areas for perfect shape control. This method results in a virtually void free frame and smoother surface inside the frame.