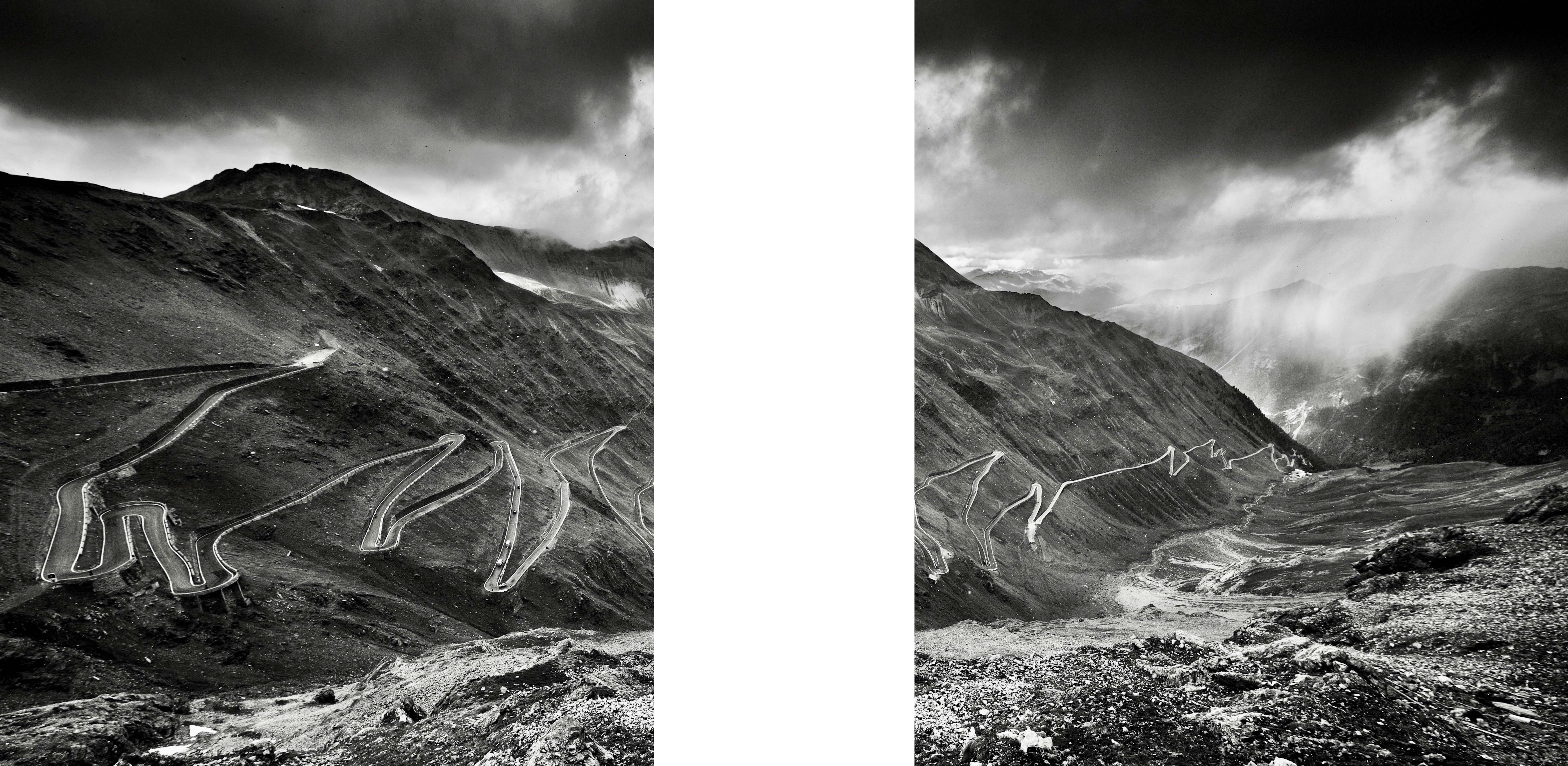
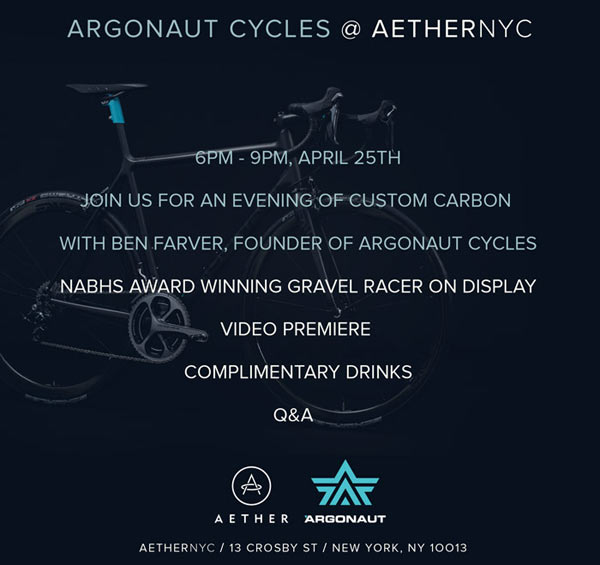
Aether Apparel NYC Store
Friday April 25th from 6-9 PM. Free drinks, a presentation from founder Ben Farver and the video premier of the Argonaut Deep South Odyssey. Our NAHBS Best In Show Gravel Racer will be on display.
A custom bike should fit like, well, a custom bike. And, it should fit without the use of an extra short or extra long stem, 4cm of spacers, or your saddle shoved all the way forward. In other words, a custom bike should look like it was made for you rather than modified to fit you. Our adjustable molds make frames ranging in size from 51cm effective TT and 100mm head tube to 61cm effective TT and 230mm head tube height, and every variation in between down to the one-hundredeth of a millimeter.
Layup Process
At Argonaut, we lay up the carbon fiber on the bladder, as opposed to in the tool. By building individual frame parts layer by layer on a rigid internal bladder, itʼs possible to achieve 360° of consistent, controlled wall thickness. Laying up parts on the bladder instead of inside the mold eliminates stress risers, and guarantees predictable road feel and handling characteristics.
Beyond ˮLight and Stiffˮ
Carbon fiber is the best custom bike material available for one simple reason: The degree to which it can be engineered and modified, in order to deliver a huge of range of performance results, is unmatched. There is much more to making a bicycle with amazing ride quality than shedding grams and beefing up the bottom bracket. You need to consider not just every tube length and frame angle, but every aspect of each tubeʼs role in the whole frame.
Adjustable Molds
The cornerstone of the Argonaut process is a set of adjustable frame molds. Weʼve engineered our tooling so that all frame angles and frame section lengths are resolved inside the tool during the molding process, rather than modifying them after theyʼve been molded. The result of this is really the Holy Grail of custom carbon fabrication: technologically sophisticated frames that are truly custom, each and every time. Youʼll never see an * after the word ˮcustomˮ on our bikes.
Bladder Molding Construction
Rather than bonding and wrapping individual carbon fiber tubes, the Argonaut frame is made up of seven molded frame sections, each with a layup pattern specific to that customer. Molding complete frame sections allows us to engineer every part of the frame to custom specifications, especially the crucial intersections. The process produces zero redundant material, and gives us complete control of the tube wall thickness.
Proprietary Technology
Argonaut frame parts are made from scratch. That means each piece starts with individual sheets of pre-impregnated carbon fiber, which together make up whatʼs called the layup pattern. The layup pattern is what determines how each frame part will perform and what characteristics it will impart to the overall ride. Layup patterns vary in terms of the amount of fiber in each pattern, the modulus of the individual fibers, and most importantly, the orientation of the fibers.